Warehousing plays a crucial role in efficient stock management and smooth logistics operations. This article explores in detail what warehousing is, why it is necessary, its advantages and disadvantages, and the associated costs.
What is storage?
Warehousing is an essential part of logistics management, encompassing a number of activities that are crucial to the success of your business. efficient management of stocks and goods flows. Here's a more detailed expansion of the storage components :
Receipt of goods : Warehousing begins with the receipt of goods from suppliers or production units. This stage involves checking that goods delivered conform to orders, quantifying incoming stocks, documenting arrivals, etc.
Storage : Once the goods have been received, they are stored in specific locations within the warehouse. Storage is organised in such a way as to optimise the use of space, facilitate access to products for order preparation and guarantee the safety of the goods. security of goods.
Order preparation : Warehousing also includes order picking, which involves putting together the items needed for each order based on customer requests. This may involve picking (product selection), the packing (product packaging) and labeling (package labelling).
Stock management : Warehousing involves rigorous stock management, including keeping up-to-date inventories, monitoring stock levels, managing rotations (FIFO, LIFO), managing out-of-date or obsolete stock, etc. Effective stock management helps avoid stock-outs and overstocking, while optimising product availability.
Distribution of goods : Once orders have been prepared, warehousing involves distributing the goods to their final destinations. This may involve the use of various modes of transport (trucks, planes, ships, trains), external logistics providers or in-house delivery services.
Maintenance and safety : Warehousing also requires maintenance activities to ensure the smooth running of facilities (equipment servicing, repairs, cleaning) as well as security measures to protect goods against theft, damage or environmental disruption.
The need for storage
Warehousing is an essential component of the supply chain, playing a crucial role in efficient stock management and smooth operations. Here is a detailed expansion of the reasons why warehousing is necessary:
Secure storage : Warehousing provides a secure environment for storing goods. Warehouses are generally equipped with security systems such as surveillance cameras, alarms and access controls, which protect goods against damage, theft or deterioration.
Stock management : Efficient warehousing enables stock levels to be managed optimally. This involves tracking incoming and outgoing goods, keeping up-to-date inventories, calculating minimum and maximum stock levels, optimising the use of space and ensuring that products are available to meet demand.
Order preparation : Warehousing makes it easier to prepare and dispatch orders. By grouping items together in one place, labelling them clearly and preparing them for dispatch, it becomes more efficient to respond to customer requests by dispatching ordered products quickly and accurately.
Effective distribution : Warehousing contributes to efficient distribution by centralising logistics operations. By grouping goods together in a single location, it is possible to reduce order processing times, improve the accuracy of shipments and coordinate delivery operations to final destinations more efficiently.
Cost optimisation : By effectively managing stocks, minimising losses due to damage or theft, and optimising the use of warehouse space, warehousing helps to reduce overall operational costs for businesses.
Benefits of warehousing
The advantages of warehousing are numerous and contribute significantly to the efficiency and competitiveness of companies in the logistics field. Here is a detailed expansion of the main benefits of warehousing:
Stock optimisation : Warehousing enables adequate stock levels to be maintained in line with demand. By monitoring stock levels, keeping inventories up to date and anticipating changes in demand, companies can avoid stock-outs that could lead to delays in deliveries, while avoiding over-stocking that ties up capital unnecessarily.
Improving efficiency : Well-organised warehousing contributes to more efficient management of logistics operations. By centralising storage, order preparation and distribution activities, it is possible to reduce processing times, minimise goods handling errors and improve order accuracy, resulting in smoother processes and shorter delivery times.
Flexibility : Warehouses offer great flexibility in terms of storage capacity and the types of goods that can be stored. Whether it's finished goods ready for shipment, raw materials awaiting processing, goods in transit or seasonal products, warehousing makes it easy to adapt storage capacity to a company's fluctuating needs.
Customer service : Effective warehousing management translates into improved customer service. By having rapid access to stock, dispatching orders quickly and ensuring product availability, companies can respond quickly to customer requests, improving customer satisfaction and building long-term loyalty.
Cost reduction : By optimising stocks, improving operational efficiency and reducing errors and delays, warehousing helps to reduce overall supply chain costs. Smoother processes also enable save on labour, transport and stock management costs.
Disadvantages of storage
Operating costs : Warehousing involves operational costs such as facility rent, labour costs, maintenance costs, etc., which can represent a financial burden for companies.
Stock management : Poor stock management can lead to additional costs associated with overstocking, stock losses, obsolescence, etc.
Limited space : Warehouses can face space constraints, which can limit their storage capacity and require logistical adjustments.
Logistical complexity : Managing warehousing operations can be complex, particularly for companies with a large number of product references, rapid turnover cycles or specific storage requirements.
Cost of storage
Warehousing costs include :
Rent and operating costs : Costs associated with renting or owning storage facilities, including electricity, heating, water, etc.
Workforce : Labour costs for receiving, storage, order preparation, inventory, maintenance, etc.
Equipment and technology : Costs of acquiring and maintaining handling, storage, stock control and safety equipment, etc.
Insurance and safety : Insurance costs to cover inventory-related risks, as well as investments in security for facilities and inventories.
Waste management : Costs associated with managing packaging waste, damaged or out-of-date products, industrial waste, etc.
In conclusionWarehousing is an essential part of the supply chain, offering many benefits in terms of stock management, operational efficiency, flexibility and customer service. However, it also presents challenges such as operational costs, inventory management difficulties and space constraints. Companies need to carefully weigh up the costs and benefits of warehousing to optimise their logistics operations and ensure effective inventory management.
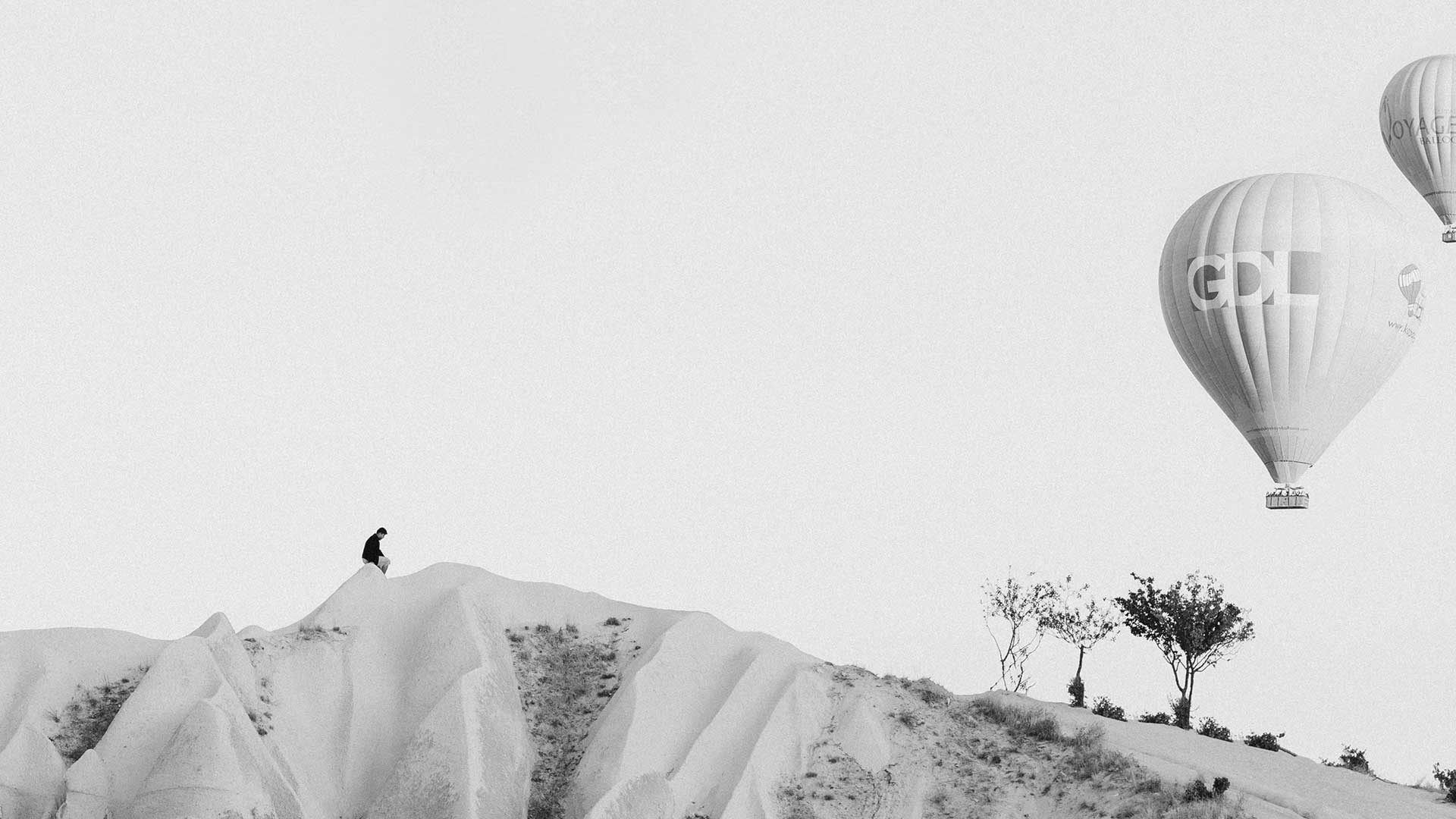
Storage
Compare quotes for your project and get the best price!