Logistics is an essential area of business, involving the efficient and strategic management of the supply chain, product storage, transportation and delivery to end customers. In this article, we will explore in detail what logistics procurement involves, why it is necessary, its advantages and disadvantages, and the costs associated with it.
What does logistics purchasing involve?
Logistics procurement is a strategic process that encompasses all the stages involved in acquiring the resources and services needed to optimise the supply chain management of a company. Here's what's involved in more detail:
Storage equipment : Logistics purchasing includes the acquisition of various storage equipment such as shelving, racks, pallets, containers, etc. This equipment is essential for organising stock efficiently and facilitating inventory management.
Warehouse management systems : This involves the purchase of software and technologies to optimise the management of warehouse operations. These include stock management systems, product traceability solutions, order management software, etc.
Transport vehicles : Logistics purchasing also includes the acquisition of vehicles suitable for transporting goods. This may include trucks, vans, forklift trucks, pallet trucks, etc. These vehicles are essential to ensure that transport and distribution operations run smoothly.
Goods tracking technologies : This involves the purchase of technologies such as GPS tracking systems, barcodes, RFID chips, etc., enabling goods to be tracked and traced throughout the supply chain. This contributes to better visibility and control of goods flows.
Research and selection of suppliers and logistics service providers: Finally, logistics purchasing also involves researching, evaluating and selecting logistics suppliers and service providers. This involves comparing offers, negotiating contracts, ensuring the quality of the services offered, etc.
The need to purchase logistics
The need for companies to purchase logistics is fundamental, and is based on a number of key factors that contribute to improving their overall performance and their market competitiveness. Here are some of the detailed reasons why:
Supply chain optimisation : Purchasing logistics enables all supply chain processes to be optimised, from stock management to product distribution. This means better visibility of stock levels, reduced costs associated with overstocking or stock-outs, and improved supply planning.
Cost reduction : By investing in efficient logistics systems, companies can significantly reduce their operational costs. This includes reducing storage costs through optimised warehouse management, transport costs through efficient route and load planning, and costs associated with delivery delays through better coordination of logistics activities.
Improving customer satisfaction: Efficient logistics management guarantees delivery fast, reliable and in line with customer expectations. This helps to increase customer satisfaction by meeting their needs in terms of delivery times, product quality and after-sales service.
Increased competitiveness : A well-managed supply chain gives a company a competitive edge by enabling it to offer superior services to its customers. Prompt delivery, timely availability of products and effective returns management all help to enhance the company's reputation in the marketplace and build customer loyalty.
Risk management : A good logistics system effectively manages the risks associated with delays, loss of goods and quality problems. By implementing rigorous monitoring and control processes, companies can reduce operational risks and guarantee the reliability of their logistics operations.
Advantages of purchasing logistics
Improving operational efficiency : A well-designed logistics system optimises a company's internal processes, from stock management to product distribution. This means more efficient use of resources, reduced order processing times and costs, and better coordination of logistics activities.
Reduced storage costs : Efficient storage solutions, such as intelligent warehouses or advanced inventory management systems, reduce the costs associated with warehousing goods. This includes minimising the costs associated with storage space, goods handling and the risks of overstocking or understocking.
Fast, reliable delivery: Well-organised logistics guarantee short, reliable delivery times for customers. Thanks to efficient route planning, optimised transport management and goods tracking processes, companies can ensure punctual, high-quality deliveries, which contributes to customer satisfaction and loyalty.
Optimised stock management : Integrated inventory management systems enable real-time monitoring of stock levels, goods movements and logistics flows. This helps to avoid overstocks or stock-outs, optimise replenishments and reduce the costs associated with overstocks or stock-outs.
Adaptability to change : Flexible, scalable logistics solutions enable companies to adapt quickly to fluctuations in demand, changes in customer preferences and market developments. This includes the ability to adjust storage capacities, modify delivery routes and optimise logistics processes in line with changing business needs.
Improving customer satisfaction: Efficient logistics management means a better customer experienceThis contributes to strengthening customer relations, building loyalty among existing customers and attracting new customers with a reliable, high-quality service. This helps to strengthen customer relations, build loyalty among existing customers and attract new customers thanks to a reliable, high-quality service.
Disadvantages of buying logistics
High initial cost : Purchasing logistics systems and equipment can represent a significant financial investment for a company. This includes the purchase of inventory management software, goods tracking systems, specialised transport vehicles, handling equipment, etc. The initial cost can be an obstacle for some companies, especially SMEs or start-ups with limited budgets.
Need for expertise : Setting up and managing effective logistics systems requires specialist skills and expertise in supply chain management. Companies need skilled people who can design, implement and supervise logistics processes, which can be a challenge in terms of recruitment and training.
Risk of technical breakdown : Computerised systems used in logistics, such as inventory management software or order tracking systems, can experience technical failures. These failures can lead to delays in order processing, errors in goods tracking or disruptions in the supply chain. Regular maintenance and rapid resolution of technical problems are essential for minimise these risks.
Management complexity : Implementing sophisticated logistics systems can add a degree of complexity to the day-to-day running of a business. Coordinating the flow of goods, managing stocks, planning transport and working with suppliers and logistics service providers all require rigorous organisation and effective communication.
Changing needs : A company's logistics needs can change over time as a result of business growth, changes in customer demand and market developments. This can require frequent adjustments to existing logistics systems or even additional investment to meet new needs, which can be costly and time-consuming.
Cost of purchasing logistics
Purchase of materials and equipment : One of the main costs associated with purchasing logistics is the acquisition of materials and equipment needed to optimise logistics operations. This can include stock management systems, order tracking software, materials handling equipment such as forklifts, conveyors or pallets, specialist transport vehicles such as refrigerated trucks or semi-trailers, and storage equipment such as shelving or containers.
Set-up and installation costs : In addition to the purchase of equipment, the costs of setting up and installing this equipment must also be taken into account. This may involve costs associated with the physical installation of logistics systems in warehouses or production sites, as well as the costs of configuring and parameterising software and IT tools.
Staff training costs : The introduction of new logistics systems may require appropriate training of staff to ensure effective and optimal use. These costs include expenditure on training programmes, awareness sessions and lost working hours during the transition period.
Maintenance and repair costs : Once logistics systems are operational, maintenance and repair costs need to be taken into account. This includes the cost of preventive maintenance to ensure the continued smooth operation of equipment, as well as unforeseen expenses associated with repairs in the event of breakdowns or malfunctions.
Management expenses for suppliers and logistics service providers : Finally, logistics procurement can also generate expenses related to the management of suppliers and logistics service providers. This includes transaction costs, contract management fees, external consultancy fees, as well as expenses associated with supervising and monitoring the performance of suppliers and service providers.
In conclusion, Logistics procurement is a strategic investment for companies looking to optimise their supply chain, reduce costs, improve customer satisfaction and enhance their competitiveness in the marketplace. Although it involves initial costs and technical challenges, the long-term benefits in terms of operational efficiency and overall performance make it an attractive option for companies looking to optimise their supply chain. essential for modern businesses.
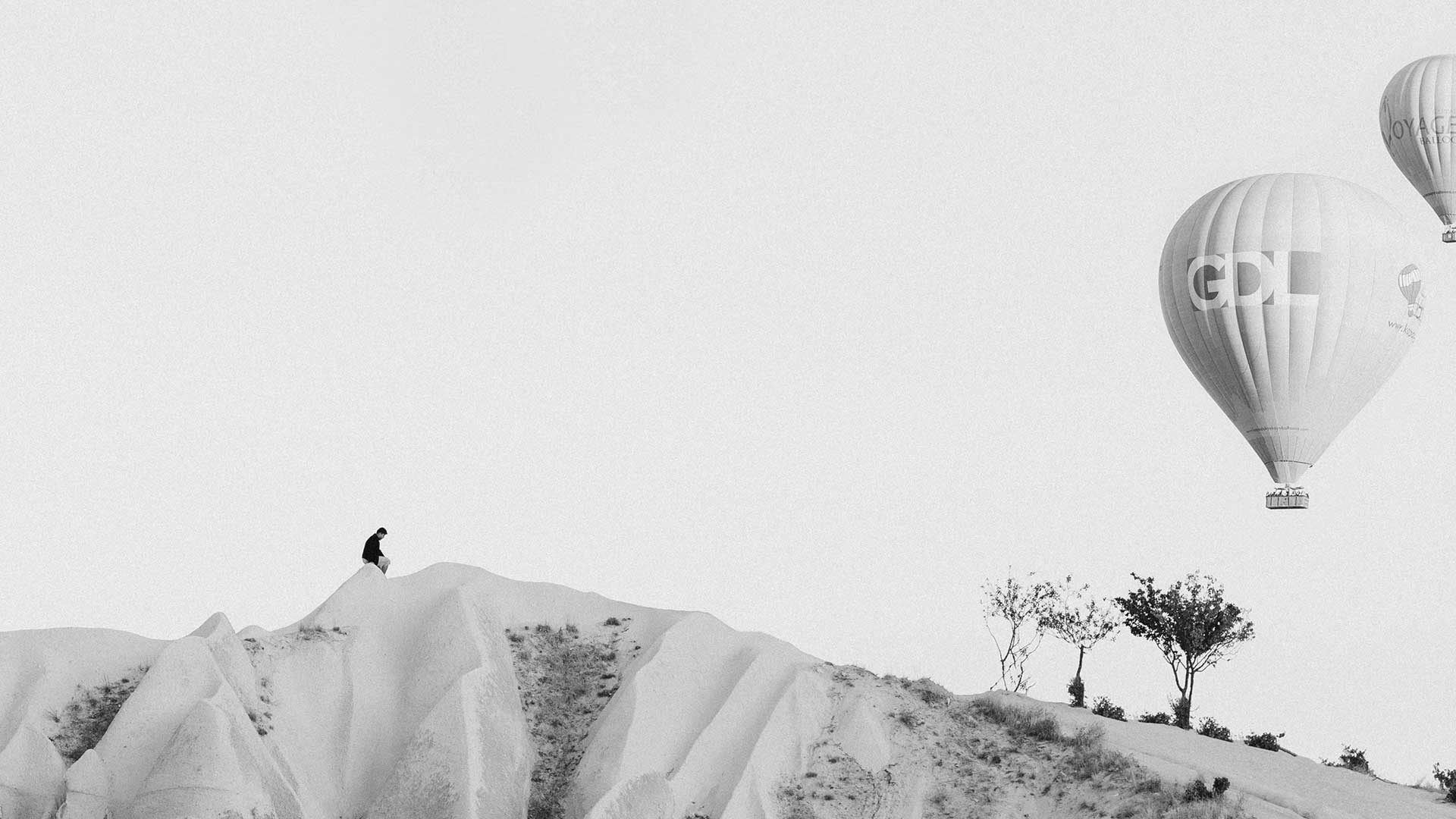
Logistics
Compare quotes for your project and get the best price!