Materials handling is an essential component of logistics operations in many industries. It involves moving, storing and handling goods efficiently and safely throughout the supply chain. In this article, we will explore in detail what materials handling is, why it is necessary, its advantages and disadvantages, and the costs associated with it.
What does handling involve?
Materials handling is a set of activities designed to move, store and handle goods efficiently throughout the supply chain. Here is a more detailed explanation of the different phases of materials handling:
1- Loading and unloading
Loading : The aim is to place goods in a means of transport such as a lorry, sea container or aircraft, taking care to position them securely and in compliance with safety standards.
Unloading : On arrival at the destination, the goods are unloaded from the means of transport. This stage often involves the use of equipment such as forklift trucks, cranes or conveyors to move the goods from the vehicle to the storage or distribution site.
2- Storage
Once the goods have been unloaded, they are placed in appropriate storage areas, such as shelving, racks, bulk storage areas, etc.
Efficient storage requires precise organisation to facilitate access to products, minimise the risk of damage and optimise the use of available space.
3- Order sorting and preparation
Triage involves classify goods based on criteria such as product type, destination, expected delivery date, etc.
Order picking involves putting together the products needed for each order using appropriate picking systems, such as picking by zone, by batch, by order, etc.
4- Shipping
Once the orders have been prepared, the goods are packaged in accordance with safety and shipping standards, ready to be dispatched to their final destination.
Shipping may involve the use of various means of transport, such as trucks, trains, ships or planes, depending on the distance and urgency of the delivery.
Necessity of handling
Handling plays a crucial role in the smooth running of logistics operations for a number of key reasons:
Optimising storage space : By efficiently organising goods in storage areas, materials handling helps to maximise the use of available space. This avoids wasting space and allows more products to be stored, which is particularly important in warehouses where space is limited.
Reducing the risk of product damage : Correct handling of goods during loading, unloading and storage helps to reduce the risk of damage. This includes the use of appropriate equipment such as pallets, secure containers and handling methods adapted to the characteristics of the products (fragile, perishable, etc.).
Speeding up the order preparation process: Efficient handling means that the products required for each order can be found quickly, thanks to logical stock organisation and optimised picking systems. This translates into reduced order preparation times, which are essential if we are to meet customer demands for speed and reliability.
Efficient response to customer requests: By facilitating the availability and rapid delivery of products, materials handling helps to meet customer expectations in terms of delivery times and product quality. This strengthens the company's reputation and builds customer loyalty.
Stock management and product rotation : Handling also enables efficient stock management by ensuring appropriate product rotation. This avoids stock obsolescence, reduces losses due to out-of-date or obsolete products, and helps maintain stock levels in line with market demand.
Advantages of Handling
The benefits of well-organised and efficient materials handling are numerous and have a positive impact on logistics operations and customer satisfaction. Here is a detailed expansion of the main benefits of materials handling:
1- Operational efficiency
Reducing waiting times: Careful planning of handling minimises waiting times between the various stages of the logistics process, helping to optimise the use of time and resources.
Optimising goods flows : Effective materials handling management creates smooth and efficient flows of goods, reducing bottlenecks and delays in the supply chain.
2- Reducing costs
Minimising loss and damage : By using appropriate handling methods, such as robust packaging and safe handling techniques, companies can reduce product loss and damage, resulting in significant cost savings.
Efficient stock management : Precise handling management helps to maintain optimum stock levels, avoiding the costs associated with overstocking or stock-outs.
3- Improving service quality
Fast, reliable delivery: Efficient handling enables orders to be prepared and delivered more quickly, which improves the company's responsiveness to customer requests and boosts customer satisfaction.
Reducing errors : Methodical organisation of handling reduces the risk of errors during order picking, ensuring greater accuracy and reliability in product delivery.
4- Increased safety
Training and adapted equipment : Proper handling management involves regularly training workers in safe handling techniques and using safe, ergonomic equipment, thereby reducing the risk of injury and improving employee well-being.
5- Flexibility and responsiveness
Ability to adapt to fluctuations in demand : Efficient materials handling enables companies to adapt quickly to variations in demand by adjusting storage, order preparation and distribution processes in line with market needs.
Disadvantages of Handling
Risk of injury: Handling activities often involve physically demanding tasks, which increases the risk of injury to workers.
Training needs : Handling operators must be regularly trained to use equipment and techniques correctly, which may require additional investment in training.
Dependence on technology : A breakdown in handling equipment or systems can cause delays and disruption to logistics operations.
Handling costs
Handling costs are important financial factors to consider when managing logistics operations. Here is a detailed analysis of the various costs associated with handling:
1- Handling equipment purchase and maintenance costs
The acquisition of handling equipment such as forklift trucks, conveyors, pallets, pallet trucks, etc. represents a significant initial investment.
Maintenance costs must also be taken into account, including repairs, spare parts, regular inspections, technological upgrades, etc. These costs are designed to ensure the smooth operation and durability of handling equipment.
2- Labour costs for operators
Salaries and benefits for handling operators represent a significant proportion of handling costs. These costs vary according to the qualifications and experience of the operators, as well as the labour regulations in force in each country.
In addition, labour costs sometimes include bonuses for tasks that are physically demanding or performed under special conditions (such as night shifts, overtime, etc.).
3- Training and safety costs
The training of handling operators is essential to ensure the safe and efficient use of equipment. The costs associated with training include instructors' fees, expenditure on training materials, travel expenses, etc.
Safety initiatives, such as the purchase of personal protective equipment (PPE), the implementation of safety procedures and regular safety audits, also have an impact on handling costs.
4- Indirect costs related to loss of goods
Damage to goods during handling may result in indirect financial losses, such as replacement of damaged products, customer claims, penalties for late delivery, etc.
These indirect costs can also include the cost of managing returns, reallocating stock and the impact on the company's reputation in the event of quality or service problems.
In conclusion, Materials handling plays a crucial role in the efficient management of logistics operations. While it offers many benefits in terms of efficiency, cost reduction and improved customer service, it also presents challenges such as health risks to workers and dependence on technology. It is therefore essential for companies to implement safe and efficient handling strategies and practices to optimise their overall logistics performance.
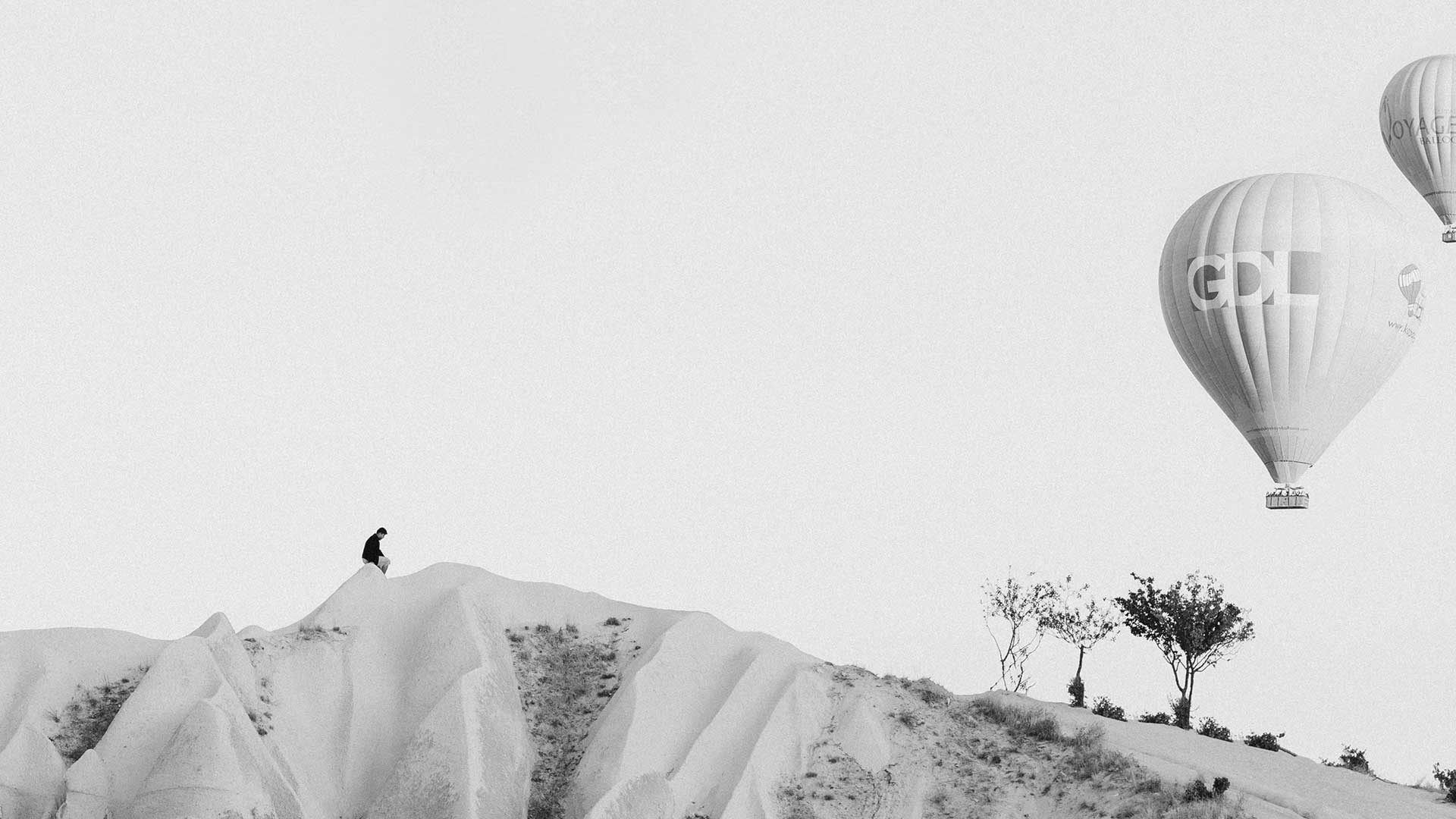
Handling
Compare quotes for your project and get the best price!