Handling, conveying and lifting are essential elements of logistics and operations management in many industrial sectors. These processes play a crucial role in moving, managing and securing goods and equipment. This article explores these three key aspects in depth, examining their importance, advantages and disadvantages, as well as the associated costs.
Explanation of Concepts
Handling : Handling refers to all the actions involved in moving and handling objects, materials or products. This can include loading and unloading goods, sorting, packaging and other similar operations.
Convoying : Conveying refers to the transport of goods from one place to another using various means such as conveyors, forklift trucks, pallet trucks, etc. Its aim is to ensure the safe and efficient movement of products throughout the supply chain.
Lifting : Lifting involves lifting heavy or bulky loads using specialised equipment such as cranes, forklift trucks, hoists, etc. This makes it possible to move objects that cannot be handled manually because of their weight or size.
Necessity of Handling, Conveying and Lifting
Handling, conveying and lifting play an essential role in the management of logistics operations for a number of crucial reasons:
Operational Efficiency : These processes optimise the fluidity of logistics operations by enabling goods to be moved quickly and securely, reducing waiting times and improving speed of delivery.
Harm Reduction : By using specialised equipment, they help to minimise the risk of accidents, product damage and injuries to workers, promoting a safer working environment.
Stock management : Handling, conveying and lifting facilitate the storage, loading and unloading of goods, enabling efficient stock management by avoiding delays and losses due to mishandling.
Increased productivity : These processes increase overall productivity by enabling the efficient movement of goods and optimising the use of human and material resources, resulting in greater profitability.
Enhanced security : By using appropriate equipment and procedures, they ensure a safe working environment, reducing the risk of accidents and injuries to workers.
Advantages of handling, conveying and lifting
The advantages of handling, conveying and lifting in logistics are numerous and contribute significantly to the efficiency and safety of operations:
Improving efficiency : These processes enable goods to be moved quickly and efficiently, reducing waiting times and delivery times. The result is greater customer satisfaction and optimised logistics flows.
Harm Reduction : By minimising the risk of accidents and damage to products, handling, conveying and lifting ensure greater safety in the workplace. This helps to create a safer working environment for employees and reduce the costs associated with incidents.
Operations Optimisation : These processes facilitate the loading, unloading, storage and transport of goods, which improves the fluidity of logistics operations. Optimal organisation of tasks also saves time and optimises the use of resources.
Improved stock management : They contribute to better stock management by enabling accurate tracking of goods movements. This helps to avoid handling errors and reduce stock losses, which in turn has a positive impact on the bottom line. company profitability.
Disadvantages of handling, conveying and lifting
Disadvantages associated with handling, conveying and lifting in the logistics field include:
High Initial Cost : The acquisition and installation of handling, conveying and lifting equipment can represent a significant financial investment for companies. This includes the purchase of the equipment itself, as well as the costs associated with its installation and integration into existing processes.
Training needs : Staff responsible for handling and using such equipment must be trained in its safe and effective use. This may require additional time and resources to ensure that employees are competent and able to work safely with this equipment.
Maintenance and Repair : Handling, conveying and lifting equipment requires regular maintenance to ensure it operates correctly and prolongs its service life. This means additional costs for preventive maintenance and any repairs required in the event of breakdown or failure.
Risk of accidents : Despite the safety measures put in place, there is always a potential risk of accidents when handling, conveying and lifting goods. This requires constant vigilance and appropriate procedures to minimise these risks.
Space occupation : Some conveyor and lifting equipment can take up a considerable amount of space in logistics facilities, which can limit storage or manoeuvring capacity in certain environments.
Cost of handling, conveying and lifting
The cost associated with handling, conveying and lifting includes the purchase or hire of specialist equipment, installation costs, staff training costs, maintenance and repair expenses, as well as indirect costs associated with managing operations. Although these costs may initially be high, the benefits in terms of efficiency, safety and productivity that they offer can often justify this investment.
In conclusion, Handling, conveying and lifting are essential elements in logistics and operational management. Their use helps to improve process efficiency, reduce handling risks, optimise stock management and ensure the smooth running of logistics operations. Although they entail initial costs, training needs and maintenance requirements, these processes remain indispensable for ensuring the safety and efficiency of logistics activities in various industrial sectors.
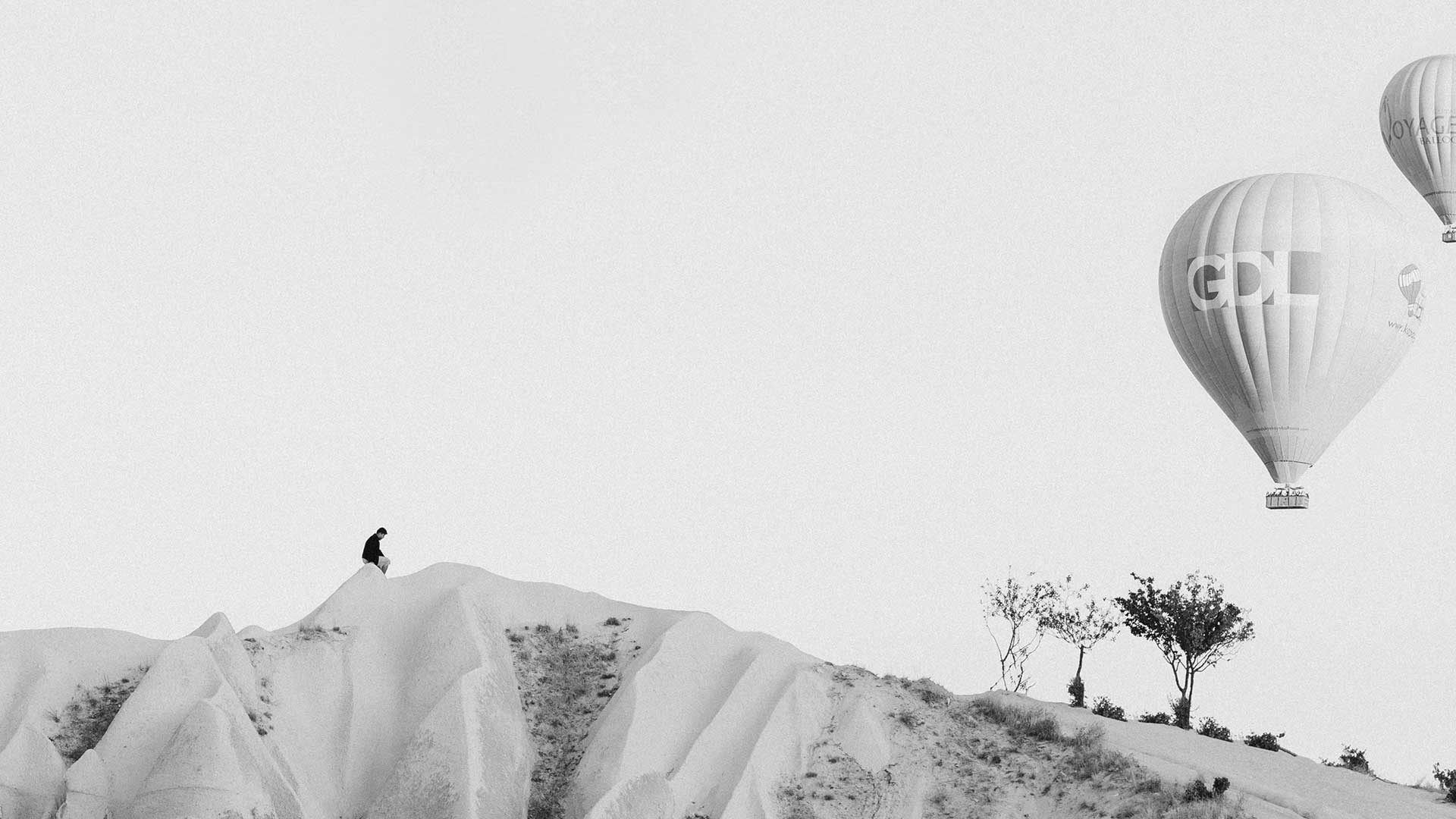
Handling, conveying and lifting
Compare quotes for your project and get the best price!